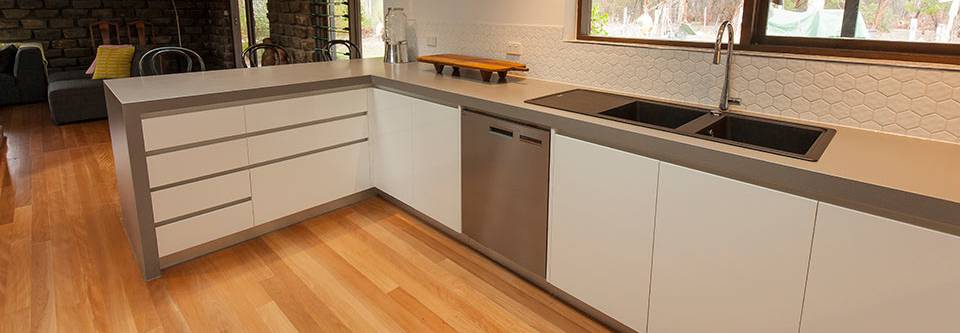
Are flatpacks any good?
Debunking misconceptions about flatpack cabinets
In the world of cabinet manufacturing, the debate between crafting cabinetry from scratch or utilising flatpacks sourced from cut-to-size manufacturers has been a long-standing topic of discussion. In this blog, we will explore the benefits of outsourcing the cutting of board to a local cut-to-size manufacturer. There are many woodworkers and cabinet makers who still feel that “Once a craftsman, always a craftsman”. They take pride in their ability to handcraft every aspect of a cabinet, from cutting the boards to assembling the final product. The reality is that wearing so many different hats is demanding and time-consuming and can have a detrimental effect on your business’s growth by not giving you the time and freedom to work on other aspects such as sales and administration. The debate over cabinetry has been ongoing. Should you invest your time and resources in producing your own cabinetry, or simplify the process by outsourcing your production requirements? It is time to dispel the negative views of flatpack cabinetry, see the many advantages below. Cabinetry cut by local cut-to-size manufacturers offers many advantages.Cost Reductions
One of the significant advantages of utilising flatpacks from local cut-to-size manufacturers is cost reduction. Cabinet makers who manufacture their own cabinetry components often face high costs including material costs, staff costs, wastage and the need for expensive machinery.Material and equipment
By having greater buying power because of the volumes that they purchase materials in, cut-to-size manufacturers can offer competitive pricing to their customers. There is no need for cabinet makers to invest heavily in expensive and specialised machinery and software as the cut-to-size manufacturer has done this. Outsourcing flatpacks has an additional benefit that the cabinet maker doesn't need to keep stock on hand. They only need to order and pay for what they require. Further to this, ordering flatpacks requires significantly less factory space. Cabinet makers who cut their own board need lots of floor space to store all stocked and ordered materials, house the CNC machine & edgebander, as well as additional factory footprint for any assembly stations. With factory space and rents being at a premium, any reduction in reliance on space would have positive financial effects for a business.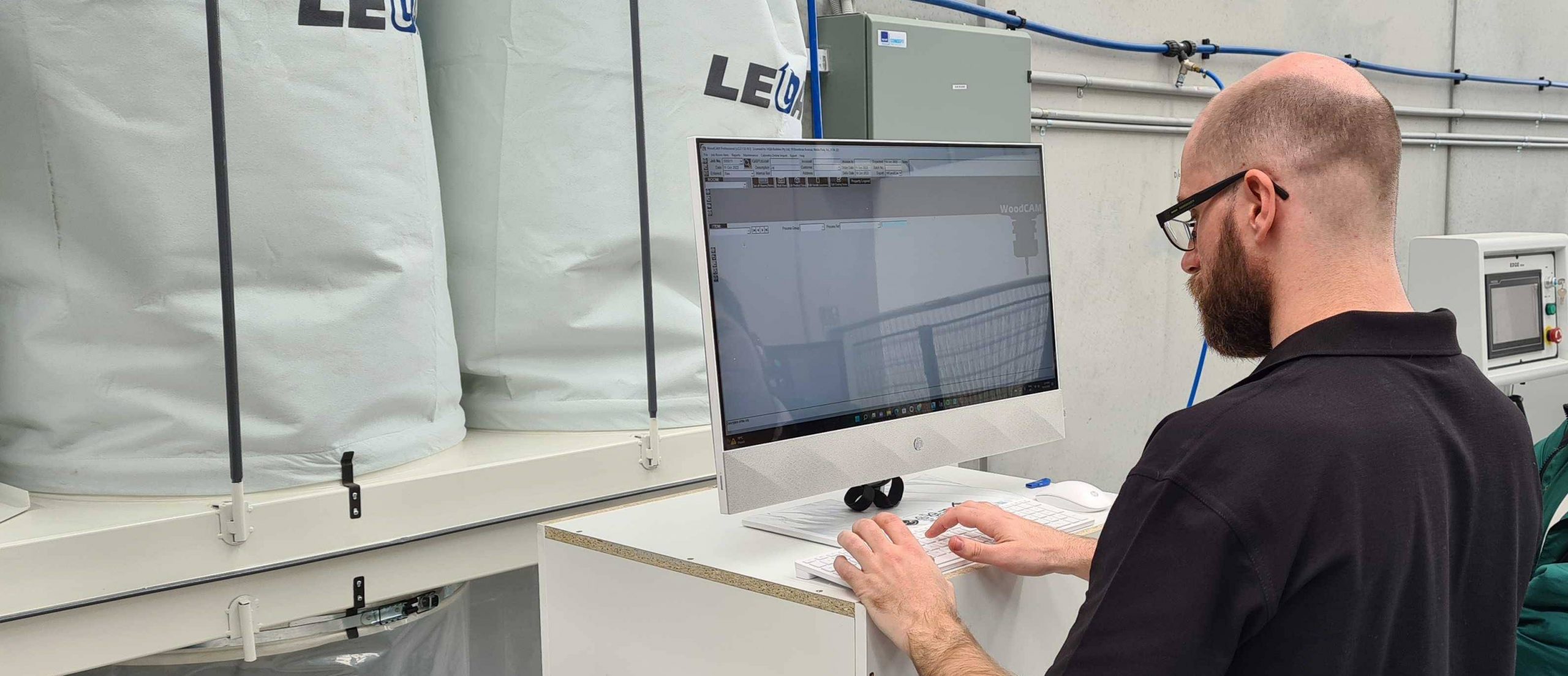
Staff costs
Outsourcing flatpacks radically reduces staffing costs. Skilled workers are currently in great demand and dividing the tasks among different specialists enhances productivity. Utilising flatpacks is the equivalent of hiring highly specialised employees at a fraction of the cost. Having multiple specialised employees on your books can be problematic and expensive: wages, taxes and super are all payable by the business regardless of whether the work is there to be done. It becomes an engine that needs to be fueled constantly by sales/work to cover the underlying costs. On the other hand with outsourcing production of cabinetry, the need for staff is diminished (say goodbye to needing a software detailer, CNC operator & factory workers - edgebanding/packing and dispatch), and these costs are wrapped in a known and easily identified quantity: the amount you pay for the job that you order.Wastage & Disposal
Flatpack manufacturers use specialised machinery and nesting software which optimises board usage. An example of this is CADCode’s TrueShape Nesting capability. Cut-to-size manufacturers using this have reported up to a 30% reduction in waste.
When manufacturing your own product, you should also be conscious of the time and cost associated with disposing of offcuts and damaged boards. From needing to pay for a bin to hold the waste (and the often exorbitant emptying fee), to the manual handling time for taking the offcuts off the router table and transporting them to the bin, the costs quickly add up. When you order your product as a flatpack, this part of the process has already been handled and you’re only receiving the componentry required for your job.
Planning and delivery
Cabinet makers who outsource their production can use an online ordering system to get live updates on the progress of their jobs. The system also provides them with completion dates. This allows the cabinet maker to plan and execute multiple jobs. Most cut-to-size manufacturers offer a delivery service. This eliminates the extra time and admin when arranging transport, which commonly ends up being more expensive. With a delivery date, other subcontractors like plumbers and electricians can be scheduled with a greater degree of accuracy and confidence.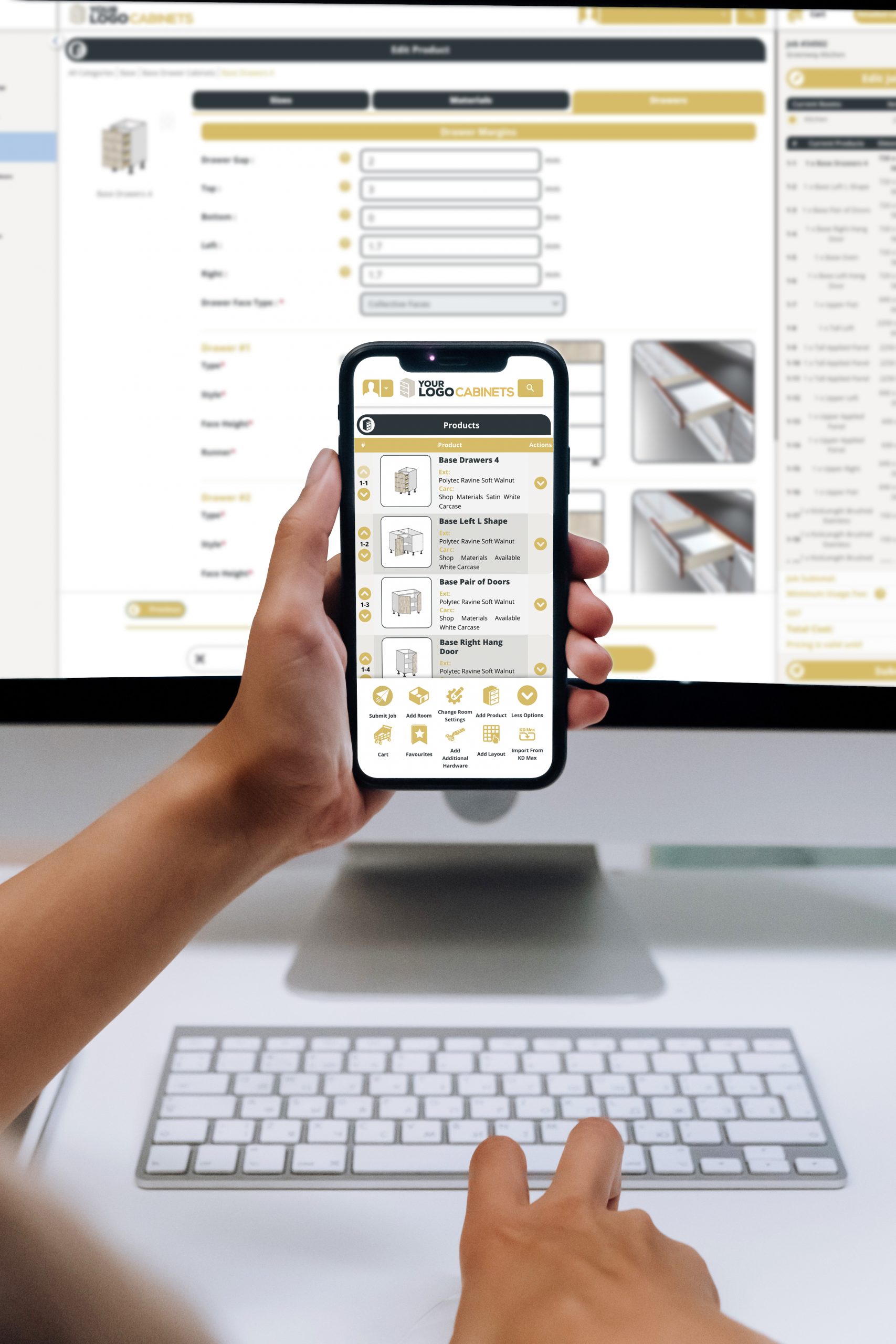
Specialisation
Focus on what you do best
Specialisation lies at the heart of every successful industry. A cabinet maker is skilled at crafting beautiful customised cabinetry. Cut-to-size manufacturers focus on precision cutting and optimising material usage. By outsourcing the cutting process, cabinet makers can focus on what they do best—designing, assembling, installing and crafting a stunning finished product for their client.Specialised tools and machinery
Cutting the boards for cabinetry requires precision and accuracy. While skilled cabinet-makers have the expertise to achieve this, cut-to-size manufacturers have specialised tools and equipment designed to achieve this at a larger scale and can normally do it in a much shorter time frame. Cut-to-size manufacturers are likely to be in closer contact with suppliers of machinery, tools and software. This enables them to stay updated on advancements and new offerings that could enhance cabinet-makers’ product lines and improve cost-effectiveness. Cut-to-size manufacturers use specialised machinery and software which eliminates the risk of human error. This results in a superior end product that meets the highest quality standards. It ensures precise and consistent cuts every time.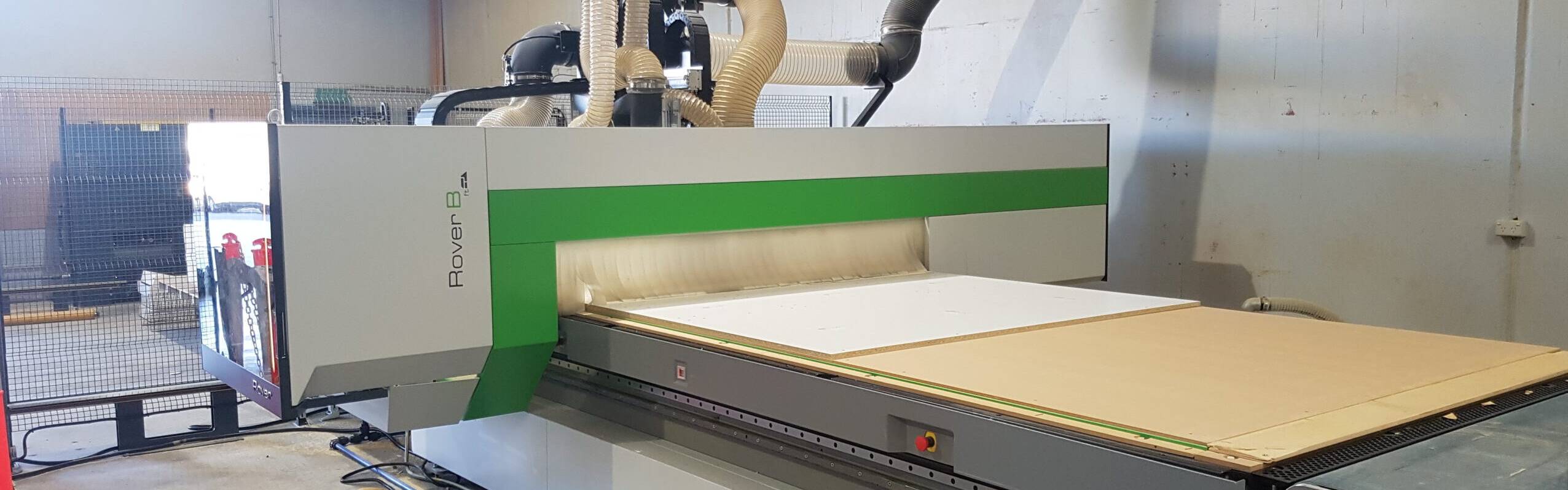
Product range
Cut-to-size manufacturers are likely up-to-date with new products and industry trends. Therefore, they’ll be able to offer a wide range of options to cabinet makers. Due to the quantity of board and hardware they require, they will also be able to negotiate preferential rates. Cut-to-size manufacturers use specialised software to operate their CNC machines. Good CAD and CAM software is constantly updating and improving. These software updates and additional add-ons include features which allow the cut-to-size manufacturer to offer specialised products.Arguments for Both Sides
While the benefits of using outsourced flatpacks are clear, it's important to consider the views of those in favour of cutting boards in-house. Some cabinet makers argue that the ability to control the entire production process ensures a higher level of quality, and ensures that the ability to meet deadlines for jobs is within their control. They also claim that the personal touch and handcrafted nature of their work sets them apart. While these arguments hold merit, it's essential to recognise that cut-to-size manufacturing can improve these qualities, not diminish them. By taking advantage of the expertise of cutting specialists, cabinet makers can achieve the best of both worlds—craftsmanship combined with precision, efficiency and scalability.Conclusion
The misconceptions surrounding flatpack cabinetry being inferior to cabinetry cut by cabinet makers are unfounded. Collaboration between cabinet makers and cut-to-size manufacturers has many advantages. Specialisation, cost reductions, and the use of specialist tools are some. So if you’re a cabinet maker considering ordering flatpacks from a local cut-to-size manufacturer to replace or complement your current production, don’t be put off by common misconceptions - flatpacks are good quality and definitely worth considering.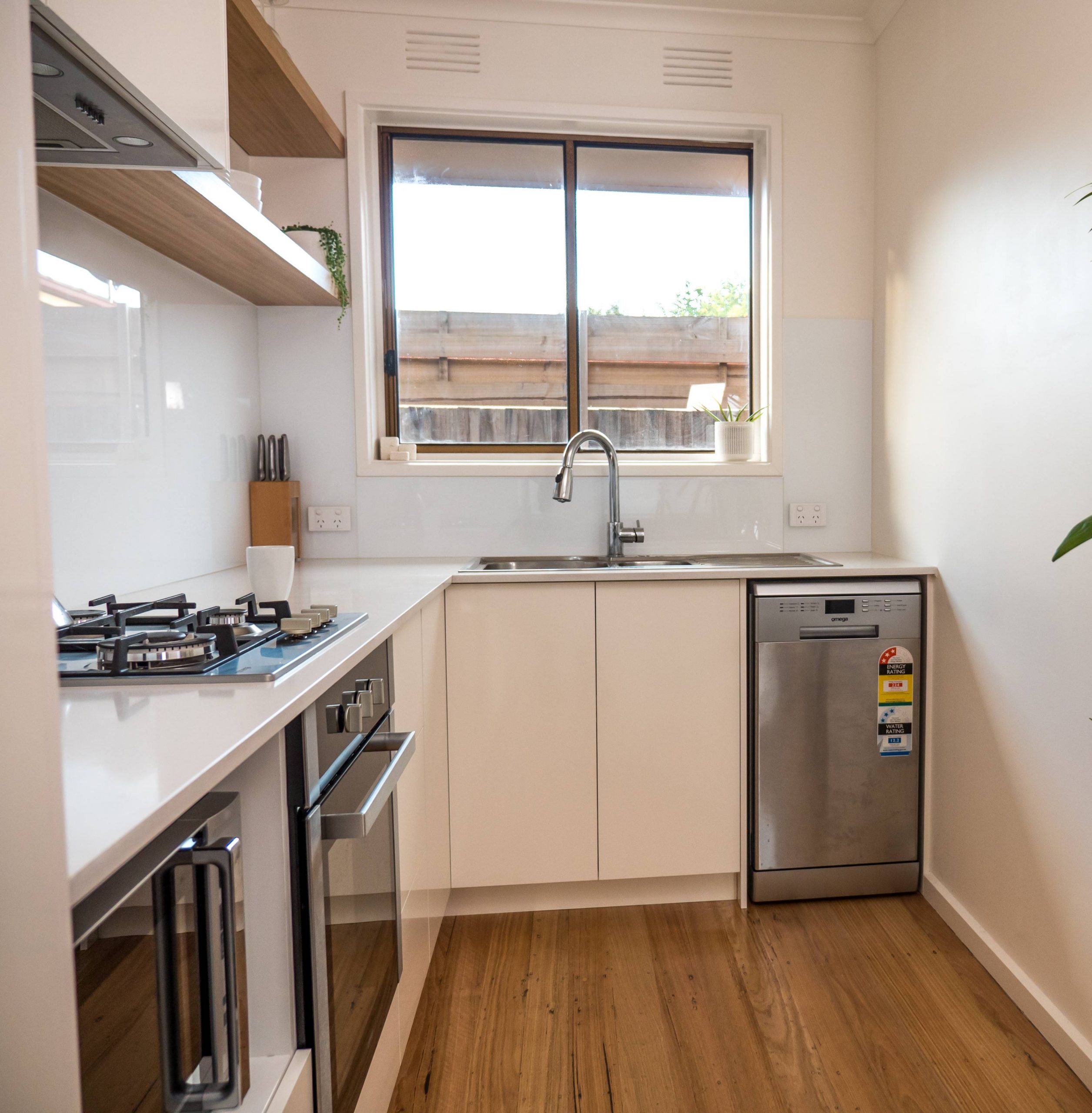